As a manager, one of your many responsibilities is to ensure that your manufacturing staff are engaged and motivated. Motivated staff will generally work harder and have higher productivity levels, which in turn increases production output and business profitability. Motivated employees are also less likely to be absent from work and staff retention levels will be higher.
However, motivating factory staff that are doing monotonous, repetitive tasks can at times be very difficult. You will also find that what motivates one member of staff won’t motivate another, so you will often need to be creative in the techniques you use, and may have to use different methods for different employees. To help with this, we have created a shortlist of 10 ways in which you can motivate your manufacturing staff.
- Lead with Vision
Leading with vision is key to motivating your staff. If you as a leader don’t lead with vision, your employees are not going to be able to see or fulfil the vision you have. Having a visual road map for the vision and frequently referring to it will enable your staff to know where they fit in the vision, and enable them to fulfil their part in it.
2. Explain the Why
When you explain the ‘Why’ to your staff, you are likely to get far higher buy-in. Asking staff to complete a task when they don’t understand the reason behind it will often result in low motivation and disengagement. Once your employees understand the benefits to themselves and the company, they will be more engaged and motivated.
3. Culture of Recognition and Appreciation
Everyone likes to be recognised and appreciated for what they do, and often it’s the small things that count the most. Showing staff that you notice and appreciate what they do helps to boost morale and engagement. Simply voicing your appreciation, or saying a simple thank you for something that a staff member has done goes a long way to motivating staff to go the extra mile in completing their day job.
4. Offer a Clear Path for Advancement
Typically, no one likes to be stuck in a dead-end job. Showing your staff that there is a clear path for advancement within the company, and working with them to set goals in relation to the career path they’d like to take, helps them to be more engaged and motivated to complete their daily activities.
5. Job Rotation
Job rotation has as twofold benefit. Rotating staff between different manufacturing roles helps to keep them motivated and reduces the risk of repetitive strain injuries as they’re not doing the same thing every day. It also provides you with a back up plan if staff are unexpectedly off ill, as you will always have more than one person on site that knows how to fulfil the role.
6. Empowerment
Empowering staff to take responsibility and make decisions themselves will have a very positive impact on their motivation. This will require training, and they may make some decisions that you don’t agree with, but if they have a clear idea of the company vision and you coach them well, they will soon become indispensable to you. With a shared vision, you will all be working towards the same goal, and there are often many different ways to reach a goal.
7. Training/Professional Development
Well trained staff are likely to perform better and be more engaged as they know what is expected of them in their role and they have been taught the skills that they need to complete the job effectively. It is also important to encourage continuous professional development in staff as this helps to stretch them and keep them engaged as they move towards new roles within the company.
8. Profit Sharing
Sharing some part of the profits with your staff is a very good way of keeping manufacturing staff engaged. If they can make an impact on their wage by what they do each day, they are likely to be far more motivated to improve manufacturing techniques and production output as they will see some financial gain from doing so.
9. Performance Related Pay
Performance related pay is a good way of keeping staff motivated. If they are able to influence how much pay they receive by the tasks they complete, they are far more likely to remain engaged with their work, and to work to the best of their ability. This also enables you as a manager to set standards and targets that are in line with the company vision and goals.
10. Scoreboard/Celebrate Wins
Having an up-to-date scoreboard that your staff can track throughout the day is key to motivating staff. If staff don’t know whether or not they’re meeting targets they will quickly become disengaged and performance levels may start to lag. Celebrating wins when they meet a target is also a key part of having a scoreboard as this helps to promote a culture where staff want to meet and exceed targets. Rewards don’t need to be huge, and can be as simple as a free lunch, or a small gift voucher.
Whilst this list is not exhaustive, these are some of the key methods which can be used to improve employee motivation. Finding what is right for your manufacturing employees will be a case of trial and error, if you try a technique and it doesn’t work, move on to the next one until you find something that does work. What works for one member of staff may not work for another, so you will need to be flexible in the techniques you use, and you may have to use a variety of techniques.
You may also find our downloadable resource pack useful as it has some tools that you can use to measure your current output and the improvement in output following the implementation of these techniques. The pack is downloadable here https://www.granta-automation.co.uk/freepack and includes an OEE calculator and basic productivity calculator amongst other useful tools.
Watch automation videos…
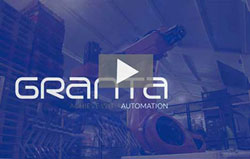