In an era of rising costs, supply chain pressure, and persistent labour shortages, businesses are turning to automation not just as a convenience, but as a necessity. Robotic palletisers are often the first step in this journey—offering an immediate solution to repetitive manual handling tasks and a straightforward ROI in the form of labour savings.
However, the true impact of robotic palletising extends far beyond cost reduction.
At Granta Automation, we’ve delivered robotic palletising systems to organisations across many different industries and we consistently see clients uncover surprising and transformative secondary benefits they hadn’t anticipated at the point of investment.
This article explores those unexpected benefits, including both tangible and intangible gains that together form a compelling case for automation that goes far beyond spreadsheets.
1. Reduced Product Damage Through Precision Stacking
Manual palletising is prone to error—misaligned boxes, uneven weight distribution, and dropped items are all too common. Over time, these mistakes can result in significant product damage, particularly in high-throughput or fragile goods operations.
Robotic palletisers offer a precision that human labour simply can’t match. With advanced programming, intelligent motion control, and accurate placement tools, these systems ensure that every product is stacked in the most stable and compact configuration possible. This reduces:
- Transit damage
- Packaging degradation
- Customer complaints
- Waste and rework
The result is a higher-quality product presentation, greater customer satisfaction, and stronger brand reputation—all of which feed back into business growth.
2. Improved Workplace Safety and Lower Staff Turnover
Palletising is a high-risk, high-fatigue task. It demands repetitive bending, lifting, and twisting, which are leading causes of workplace injury. These injuries cost businesses through time off, compensation claims, and rising insurance premiums.
By automating these tasks, businesses dramatically improve workplace safety. Employees are freed from repetitive strain and can be redeployed to less hazardous, more fulfilling roles. This leads to:
- Fewer injuries and near-misses
- Reduced absenteeism
- Better staff morale
- Lower recruitment and training costs
In an industry where employee retention is often a challenge, this shift makes a substantial difference.
3. Maximised Space Utilisation with Smarter Pallet Configurations
One of the underappreciated advantages of robotic palletisers is their ability to optimise every square metre of storage space. Manually stacked pallets often vary in height and stability, leading to inefficient use of racking and transportation space.
Robotic systems, by contrast, create uniform, dense, and stable pallets every time. This has direct implications for:
- Warehouse storage capacity
- Racking system efficiency
- Container and lorry fill rates
- Floor space for operational activities
By improving stack quality, robotic palletisers help you do more with less—freeing up space, reducing warehouse costs, and supporting a more scalable operation.
4. Built-In Scalability for Future Growth
Growth brings challenges. As demand increases, relying on manual labour to scale up production becomes a limiting factor. Labour markets are tight, training takes time, and inconsistency creeps in as volumes increase.
Robotic palletisers are inherently scalable. Modular in design, they can be adapted to handle:
- Higher throughput
- New product types or sizes
- Multi-line palletising
- Integration with other automation systems
This means businesses can respond to new opportunities without being constrained by workforce limitations—a competitive advantage in fast-moving markets.
5. Enhanced Consistency and Quality Control
Whether you’re dealing with pharmaceuticals, food, or high-value industrial goods, consistency is non-negotiable. Robotic palletisers ensure the same quality and accuracy on the 10,000th pallet as on the first.
They can also be integrated with vision systems, barcode scanners, and quality assurance software to monitor:
- Correct product orientation
- Barcode accuracy
- Packaging damage detection
- Label presence and positioning
This allows for real-time quality control at the point of packaging—eliminating errors before they become customer problems.
6. Operational and Energy Efficiency
While labour savings often drive investment, energy savings can significantly add to long-term ROI. Robotic palletisers are energy efficient, running only when required, and consuming less power per cycle compared to legacy machinery or inconsistent manual operations.
They also contribute to leaner, more efficient workflows by integrating seamlessly with conveyors, sensors, and smart scheduling systems.
7. Access to Real-Time Data and Performance Monitoring
Modern robotic systems generate vast amounts of actionable data. This includes:
- Number of pallets completed
- Cycle times and efficiency
- Error logs and downtime alerts
- Predictive maintenance prompts
This data enables better decision-making and proactive maintenance, ensuring the palletising line continues to run efficiently without costly interruptions.
8. The Often Overlooked: Intangible Benefits That Drive Real Value
While measurable benefits are critical for justifying capital expenditure, intangible benefits often deliver the most lasting impact. These are the improvements that change how your team works, how your customers perceive you, and how confidently you can plan for the future.
Based on our extensive work with clients, here are some key intangible benefits that robotic palletising provides:
- Reduced Workplace Stress
When staff are no longer burdened with physically demanding, repetitive tasks, stress levels drop. Supervisors no longer have to deal with daily staffing issues, fatigue-related errors, or health and safety concerns. The entire environment becomes calmer, more focused, and more resilient.
- Improved Customer Perception
Consistent, well-packaged pallets improve how customers view your professionalism and product care. Deliveries arrive intact and correctly labelled—helping to build trust and secure repeat business.
- Greater Confidence in Meeting Deadlines
With robotic palletisers in place, there’s less risk of production delays due to absenteeism or manual bottlenecks. This gives your operations team more confidence in hitting dispatch targets, and gives your sales team confidence to promise delivery timelines.
- Enhanced Team Morale
By automating mundane tasks, staff are reassigned to more meaningful roles—often involving equipment oversight or process improvement. This investment in people as well as technology leads to higher morale and stronger team engagement.
- Reduced Management Burden
Fewer operational fires to fight means more time spent on strategic planning, process improvement, and growth initiatives. Managers benefit from smoother operations and more predictable performance.
Final Thoughts: Robotic Palletisers as Strategic Enablers
While labour savings may be the trigger for considering robotic palletising, they are rarely the most valuable outcome. Companies that embrace automation quickly realise they’ve invested in:
- Improved quality
- Increased safety
- Higher throughput
- Greater consistency
- Scalable growth capacity
- Improved workplace culture
- Elevated customer experiences
At Granta Automation, we design and deliver custom palletising systems that address the full scope of your operation—not just your labour line item. Our solutions are built for performance, flexibility, and long-term return on investment, incorporating the tangible and intangible benefits that drive modern manufacturing excellence.
👉 Learn how automation can transform your operations—ask for a link to our customer testimonials!
From high-volume manufacturers to niche producers, our systems are making a measurable impact—see what’s possible when you go beyond labour savings.
If you would like to know more about the Granta palletising systems or AMR/AGV systems, then please do get in touch on 01223 499488 or contact us at helpline@granta-automation.co.uk. We will be very happy to help.
Watch automation videos…
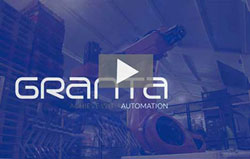
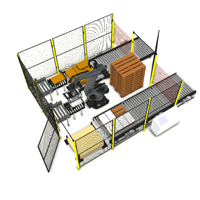
Bag Palletiser
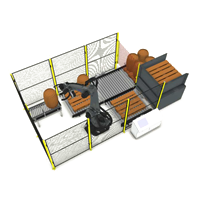
Barrel Palletiser
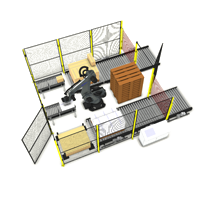
Box Palletiser
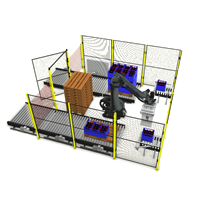
Crate Palletiser
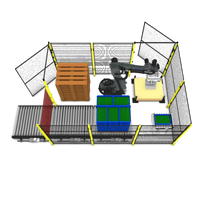
Tray Palletiser