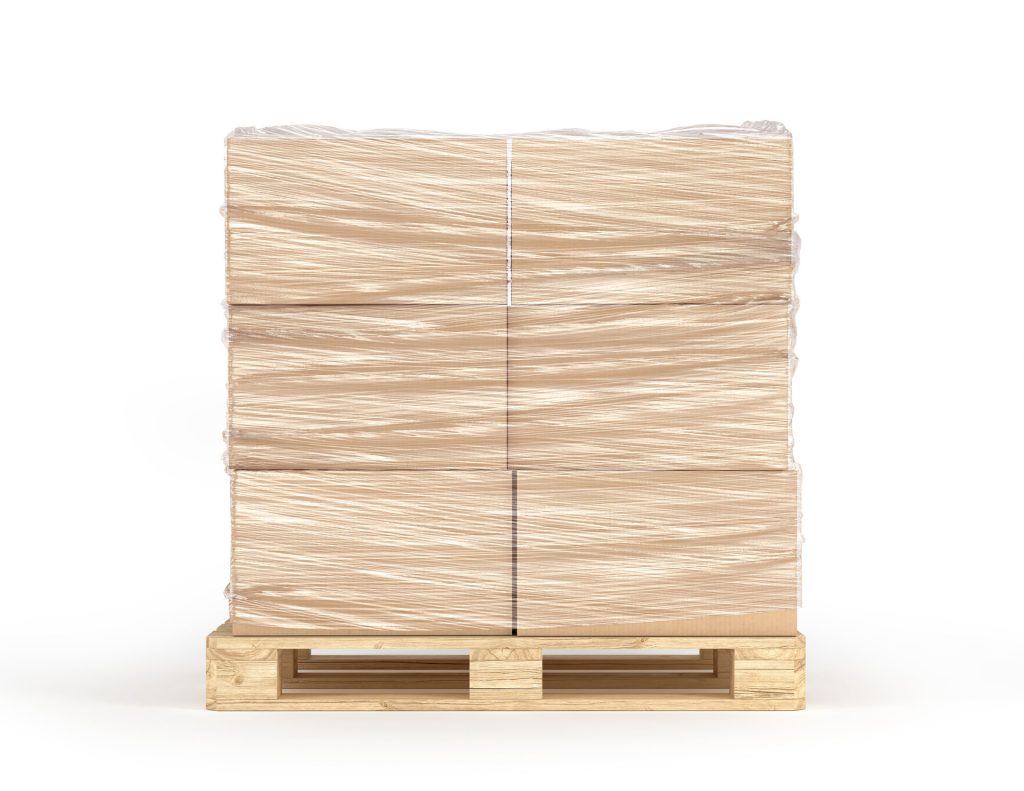
Manual palletising, where workers physically stack products onto pallets, is a staple in many industries due to its flexibility and straightforward approach. However, it’s also fraught with challenges that can hinder efficiency, increase costs, and put workers at risk of injury. While manual palletising has its place, the growing demand for higher productivity, consistency, and safety has led many businesses to explore automation as a solution. In this article, we’ll dive into the common efficiency problems associated with manual palletising and discuss how integrating automated palletising systems can help overcome these challenges and optimise operations.
Common Manual Palletising Efficiency Problems
1. Inconsistent Product Placement
Inconsistent product placement is a frequent issue in manual palletising that can lead to unstable loads, increased risk of product damage, and inefficient use of pallet space. These inconsistencies arise from human error, fatigue, and the absence of standardised procedures.
Causes:
- Human Error and Fatigue: Variations in stacking due to worker fatigue or differing techniques.
- Lack of Standardised Procedures: Without clear guidelines, workers may develop their own methods, leading to uneven stacking.
Solutions:
- Implement Standardised Stacking Guidelines: Establish clear protocols for stacking to ensure uniformity.
- Adopt Automated Palletisers: Automated systems can eliminate inconsistencies by precisely aligning and placing products on pallets. These machines are programmed to follow specific stacking patterns, ensuring every pallet is uniformly packed, reducing the risk of load instability and product damage.
2. High Labor Costs and Productivity Issues
Manual palletising is labour-intensive, with costs rising as demand increases. Productivity can vary significantly among workers, leading to inefficiencies and potential bottlenecks.
Causes:
- Varied Worker Speeds: Different workers have different paces and efficiencies.
- Physical Limitations and Fatigue: The repetitive and strenuous nature of the work can slow down productivity.
Solutions:
- Optimise Workforce Allocation: Assign tasks based on strengths to balance productivity.
- Implement Automated Palletisers to Reduce Labor Costs: Automated systems can handle the repetitive and physically demanding tasks of palletising, significantly reducing the need for manual labour. This not only cuts down on labour costs but also ensures a consistent and high productivity level, as machines can operate at a steady pace without fatigue.
3. Bottlenecks in Production Flow
Bottlenecks occur when the speed of manual palletising cannot keep up with the rest of the production line. This leads to delays, increased lead times, and overall reduced efficiency.
Causes:
- Mismatch Between Production and Palletising Speed: Manual palletising often can’t match the speed of automated production lines.
- Inefficient Workflow Design: Poor layout and organisation slow down the process.
Solutions:
- Balance Production and Palletising Speeds: Adjust workflow and staff levels to align speeds.
- Synchronise with Automated Systems: Automated palletisers can be calibrated to match the speed of your production line, virtually eliminating bottlenecks. These machines can handle high-speed operations, ensuring that products are palletised as quickly as they are produced, thereby maintaining a seamless flow in the production process.
4. High Risk of Injury
The physically demanding nature of manual palletising puts workers at a significant risk of injury, particularly when lifting heavy items or performing repetitive motions. Injuries can lead to downtime, increased workers’ compensation costs, and a loss of skilled labour.
Causes:
- Repetitive Strain: Continuous lifting, bending, and twisting can cause injuries.
- Improper Lifting Techniques and Overexertion: Lack of proper training and the pressure to work quickly can lead to accidents.
Solutions:
- Provide Ergonomic Training and Tools: Train workers on proper techniques and provide aids like lifting tools.
- Minimize Injury Risk with Automation: By automating the palletising process, you significantly reduce the physical strain on workers. Automated palletisers handle the heavy lifting and repetitive tasks, which greatly decreases the risk of workplace injuries. This not only protects your workforce but also reduces downtime and associated costs from injury-related absences.
5. Inefficient Use of Pallet Space
Inefficient stacking during manual palletising can lead to wasted pallet space, resulting in increased transportation and storage costs. Improper stacking patterns may also lead to unstable loads, risking product damage.
Causes:
- Lack of Consistent Stacking Patterns and Planning: Without standardised approaches or pre-planned layouts, space is often wasted.
- Product Variability: Different product sizes and shapes complicate uniform stacking.
Solutions:
- Standardize Stacking Patterns and Plan Layouts: Train workers to follow optimised stacking patterns.
- Optimise Space Utilisation with Automated Palletisers: Automated systems use advanced software to calculate the most efficient stacking patterns, ensuring maximum use of pallet space and stable loads. These machines can adjust for product variability, creating optimised stacks that reduce the number of pallets required and lower transportation and storage costs.
6. Fatigue and Reduced Productivity Over Time
Manual palletising is exhausting work, and as workers tire, their productivity and the quality of their work decline. Fatigue can also lead to mistakes and accidents, further reducing efficiency.
Causes:
- Physical and Mental Exhaustion: Repetitive and physically demanding tasks lead to quick fatigue.
- Monotonous Tasks and Long Shifts: Extended periods without rest reduce productivity and increase the likelihood of errors.
Solutions:
- Ensure Adequate Rest Periods and Rotate Tasks: Implement regular breaks and rotate tasks to reduce fatigue.
- Increase Productivity with Automation: Automated palletisers can operate continuously without suffering from fatigue, ensuring a consistently high level of productivity. By handling the most physically demanding tasks, automation allows your human workforce to focus on more skilled, value-adding activities, improving overall operational efficiency.
Manual palletising, while still widely used, comes with numerous challenges that can hinder efficiency, increase costs, and pose risks to workers. Inconsistent product placement, high labour costs, bottlenecks, injury risks, inefficient pallet space usage, and worker fatigue are just some of the issues that can arise in a manual system.
While there are strategies to mitigate these problems, such as implementing standardised procedures, optimizing workflows, and investing in ergonomic tools, integrating automated palletising systems can offer more comprehensive and long-term solutions. Automation not only addresses the specific challenges of manual palletising but also enhances overall productivity, reduces operational costs, and creates a safer work environment.
If you would like to know more about the Granta palletising systems, then please do get in touch on 01223 499488 or contact us at helpline@granta-automation.co.uk. We will be very happy to help.
Warning: Undefined variable $aria_req in /var/www/granta-automation.co.uk/news/wp-content/themes/twentyten/comments.php on line 81
Warning: Undefined variable $aria_req in /var/www/granta-automation.co.uk/news/wp-content/themes/twentyten/comments.php on line 86