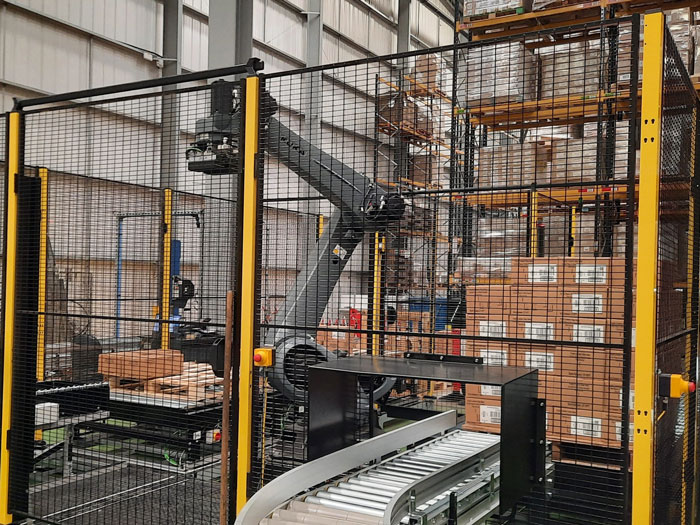
With cobot palletisers becoming more commonplace in the market, they are often confused with industrial robotic palletisers. So, what exactly is the difference between a cobot palletiser and industrial robotic palletiser? And what are the pros and cons of the two types of system?
The term cobot is short for collaborative robot; these robots may also be referred to as desktop robots. The key difference between collaborative robots and standard industrial robots is the fact that collaborative robots have been designed with inbuilt sensors and force monitoring systems that allow them to work more safety alongside humans. As a result, cobots are typically a lot smaller than industrial robots, have lower payloads, and work at slower speeds; as this enables them to stop safely if they come into contact with a human. One of the common myths about cobots is that they don’t require guarding or safety fencing. This is true in instances where the cobot is picking and placing very lightweight objects very slowly or doing a very low force movement very slowly. However, if the cobot is lifting any weight (e.g. 5Kg) or moving at the normal speeds required for palletising, it does technically require area scanners or guarding similar to an industrial robot to enable it to meet the machinery directive safety standards. This is due to the fact that the forces required for lifting items are enough to result in pinch points as items are placed on the pallet that could cause harm to humans. Also, the stopping times are not fast enough at higher speeds to meet the machinery directive. As a result, cobot palletiser installations should always be assessed in accordance with the machinery directive, be risk assessed, and normally have guarding or area scanners installed to meet the requirements for forces and stopping times.
Cobot Palletiser Disadvantages
There are two key disadvantages of a cobot palletising system; payload and speed restrictions. Different systems will have different payloads, but typically a cobot will have a low payload and will therefore only be able to lift lightweight products. A cobot will run at slower speeds than an industrial robot, which may mean that a cobot palletising system is not able to run at the speeds required to suit your production process, and you could end up creating a palletising bottleneck if you use a cobot palletiser. Typically, a cobot palletiser will only be able to pick and place using a vacuum gripper as most other types of gripper would exceed the payload of the robot, so a cobot palletiser may not be suitable for some types of products. Cobot palletisers are unable to palletise products where an underneath gripper is required due to the fact that the weight of an underneath gripper is usually more than the weight the cobot can lift. Due to the short reach of the cobots they can normally only palletise from one production line. Also, slipsheets cannot easily be used as the system typically does not have enough reach to pick and place them. Unless you are palletising very lightweight items, the cobot will require area scanners or safety guarding, which will require an area of approximately 2-3 square metres.
Cobots typically are built very lightweight to enable them to detect small forces during movement and enable them to stop in time. This means that they have a shorter working life than standard industrial robots and are less reliable. They are also often less precise in their movements, and have less accuracy and repeatability than most industrial robots.
Cobot Palletiser Advantages
Cobot palletisers can be good when you are palletising lightweight products at modest speeds. They are typically small and use a minimal amount of floor space. Typically, a cobot palletiser will be able to pick and place boxes onto two pallet positions. Some cobot palletising systems are able to handle both euro and standard pallet sizes, but it is worth checking this as not all are able to. Most cobot palletisers will have some form of fairly simple programming software that enables you to program the palletiser pick and place positions, and stack patterns. This usually involves teaching the cobot the pick and place points for each item on a palletising layer, and then duplicating and rotating each layer to create a complete pallet stack pattern. Creating these pallet stack patterns is usually quite time consuming in the first place, but they can typically be stored and reused. Providing it meets your speed and weight requirement, a cobot palletising system is sometimes a lower cost solution.
Industrial Robot Palletiser Disadvantages
The key disadvantage of a robotic palletising system is that there is no option to run the system slowly with light weights in order for humans to work alongside. A robotic palletising system will often require a bit more space than a cobot system and will sometimes require a higher initial capital outlay than a cobot palletising system. In many but not all instances, robots require more skill and time to set up and program.
Industrial Robot Palletiser Advantages
They key advantages of an industrial robot palletising system are the fact that they are more versatile and can take higher payloads. As a result, they are able to palletise higher payloads at faster speeds than a cobot palletiser. There are many different gripper options available for picking and placing product, and it is rare that a robotic palletiser will not be able to palletise at the same speed or faster than your production process. The many different gripper options allow the palletiser to palletise a large variety of products such as: boxes, display boxes, bags, trays, bottles, sacks, drums, open top crates, shrink wrapped items, cans, etc. Where high speeds are required row gripping or layer forming palletiser grippers can be used to increase the number of products being picked and placed at a time. Robotic palletisers can also be designed to work autonomously without any human input, ejecting full pallets once complete without stopping the palletising process. If you choose a robotic palletising cell that has easy programming software, your factory staff will be able to program the robot for different size products and stack patterns a lot faster than a cobot system. A robotic palletising system can also be used to palletise off multiple lines simultaneously – even if the different lines have different types of products coming off them. Typically, the payback time on a robotic palletising system is very fast, and as a rule of thumb, if you have the equivalent of one person employed full time for palletising, there is payback in less than 2 years.
Robotic palletisers are also built a lot more sturdily than cobots with more accuracy, repeatability, and strength to payload ratio; as a result, they have a longer working life with less faults.
As you can see, there are advantages and disadvantages for both cobot palletisers and robotic palletisers and it is important to consider what you wish to achieve before deciding which type of palletiser is best for your application. Some key points to consider when making a choice as to which type of palletiser to purchase include;
- What floor space is available?
- Will the system be able to meet the required cycle time?
- Do you want it to be able to run the system faster in the future if production increases?
- What future requirements are there for different types of products?
- Do you need to be able to stack off multiple production lines?
- What weight is the product being palletised?
- Can the product be vacuum picked?
- Is lifetime of the robot an important factor?
- How important is accuracy?
There are also some helpful tools that have been created to enable you to calculate the ROI of investing in a palletising system and the links to download these are below:
- Automation Payback Calculator https://www.granta-automation.co.uk/automation-project-payback-calculator
- Intangible Benefits Calculator https://www.granta-automation.co.uk/news/how-to-define-the-value-of-intangible-benefits/
- 2 Calculators to Measure the Productivity, Effectiveness or Efficiency of your Machinery or Factory https://www.granta-automation.co.uk/news/2-ways-to-measure-the-productivity-effectiveness-or-efficiency-of-your-machinery-or-factory/
If you would like any further information on cobot or industrial robot palletising systems then feel free to get in touch with us on 01223 499488 or contact us at helpline@granta-automation.co.uk.
>
Warning: Undefined variable $aria_req in /var/www/granta-automation.co.uk/news/wp-content/themes/twentyten/comments.php on line 81
Warning: Undefined variable $aria_req in /var/www/granta-automation.co.uk/news/wp-content/themes/twentyten/comments.php on line 86