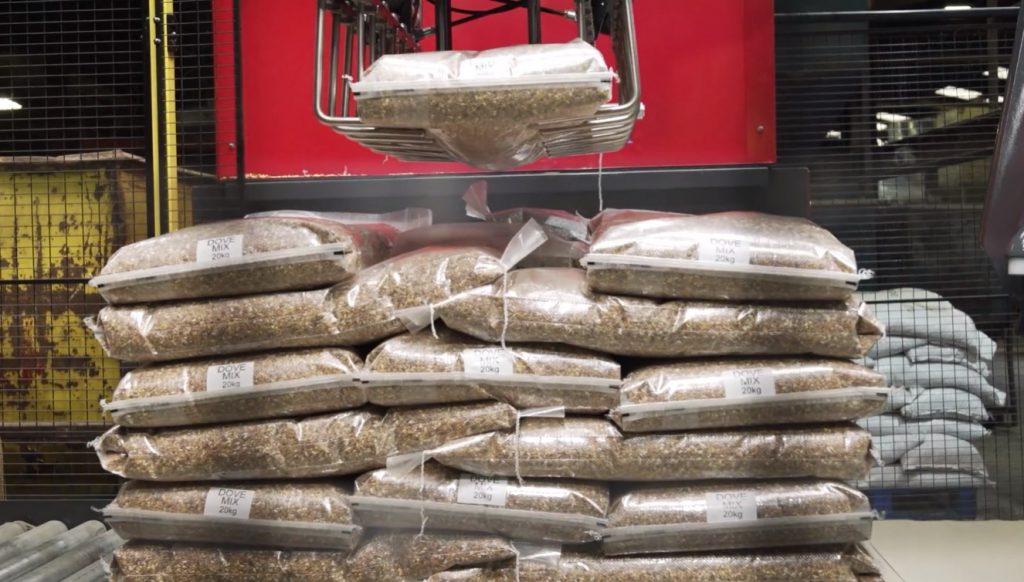
Manufacturing is evolving at a faster pace than ever before. The combined pressure of global supply chain disruptions, increasing product complexity, labour shortages, and the relentless demand for faster throughput is pushing manufacturers toward smarter, more agile production strategies. In this high-stakes environment, companies that continue to rely on manual, outdated processes are at risk of falling irreversibly behind.
One area that has seen a rapid and impactful shift is end-of-line automation—specifically robotic palletising. Once seen as a luxury investment for large operations, robotic palletising is now a practical, scalable solution that delivers immediate ROI while paving the way for long-term competitiveness.
In this article, we’ll examine why robotic palletising is more than a tactical upgrade—it’s a strategic necessity. We’ll look at the rising demand for automation across the sector, how robotic palletising systems are designed for seamless integration and how automation equips manufacturers to adapt and thrive in a rapidly changing industrial landscape.
The Growing Demand for Automation in Manufacturing
Over the last decade, automation has shifted from being a tool of efficiency to a lifeline for continuity and growth. In a world where product mixes change rapidly, customer expectations for shorter lead times intensify, and access to skilled labour is increasingly constrained, manufacturers are being forced to rethink how they structure their production lines.
Robotic palletising offers a powerful solution to many of these challenges. It eliminates manual handling errors, reduces workplace injuries, enhances consistency in pallet formation, and can operate continuously with minimal supervision. With many plants operating multiple shifts to meet demand, having a system that doesn’t fatigue, doesn’t require breaks, and performs with unwavering precision becomes a clear competitive advantage.
Beyond efficiency, automation is becoming a prerequisite for meeting customer compliance requirements. Retailers and distributors are increasingly setting stricter standards for pallet quality, labelling accuracy, and load stability. Robotic palletisers help ensure that every pallet leaving your facility meets these standards without exception.
Global spending on industrial robots in the packaging and palletising sector has increased year on year, with SMEs now representing one of the fastest-growing segments in automation adoption. The message is clear: automation is no longer confined to mega-factories—it’s a vital asset for operations of every size.
Seamless Integration: From Legacy to Leading-Edge
One of the lingering myths around robotic palletising is that it’s disruptive to implement. In reality, modern palletising systems are designed to integrate quickly and cleanly with existing infrastructure—whether you’re working with legacy machinery or the latest production technology.
At the heart of this easy integration is system design. Robotic cells are now built with flexibility in mind: compact footprints, adjustable infeed and outfeed conveyor heights, and custom end-of-arm tooling ensure that they can slot into existing production lines with minimal reconfiguration. Many systems can be installed and commissioned within a matter of days, drastically reducing any potential downtime.
Communication between systems has also become significantly more seamless. Robotic palletisers can now ‘talk’ to upstream equipment (such as case erectors or labellers) and downstream logistics systems (like AGVs or stretch wrappers) with ease. This connectivity not only ensures smooth operation but also opens the door to real-time process synchronisation.
Furthermore, user-friendly interfaces such as Granta Automation’s easy programming software have replaced the complicated programming environments of the past. Today’s HMIs are designed for operators, not programmers. That means a shift supervisor can teach the robot a new product pattern or diagnose a fault in minutes—without calling in an engineer.
Agility Through Automation: Thriving Amid Change
In today’s climate, adaptability is more than a strategic advantage—it’s a survival skill. Manufacturers are expected to pivot quickly in response to everything from market fluctuations to global crises. Whether it’s a sudden change in packaging regulations, an urgent shift in product mix, or a rapid scale-up due to new contracts, flexibility is key.
Robotic palletising gives manufacturers the ability to respond without overhauling their entire production line. For example, changes in SKU dimensions can managed simply with the easy programming software from Granta Automation. Anyone can reprogram the palletiser for new product sizes or stack patterns within just a matter of minute. A surge in output can be absorbed by running the robot longer hours without compromising accuracy. Even layout reconfigurations—such as moving a line to accommodate a new machine—can be achieved more easily when your palletising is modular and mobile.
In addition, automation helps companies remain compliant and forward-thinking. As environmental and sustainability regulations tighten, companies are being asked to use lighter, more recyclable materials—which often behave differently during stacking. Robotic palletisers equipped with smart sensors and adaptive grippers can handle these delicate loads better than manual operators or older fixed automation systems.
And finally, consider the impact on your workforce. While automation reduces the need for repetitive manual labour, it also elevates the roles of existing staff. Operators become system supervisors, responsible for optimisation and oversight, rather than physical execution. This shift not only improves morale and retention but also fosters a culture of continuous improvement.
Conclusion: A Strategic Imperative, Not a Technical Upgrade
As the manufacturing landscape becomes more complex and demanding, the need for smart, scalable solutions is undeniable. Robotic palletising addresses immediate operational pressures while delivering a foundation for long-term agility and scalable growth.
It’s more than a productivity tool—it’s a strategic asset that empowers manufacturers to future-proof their operations. From seamless integration to adaptable performance, robotic palletising is transforming how factories run, how teams work, and how businesses compete.
For those ready to lead, the time to automate is now. Contact us today for a quote on 01223 499488 or email helpline@granta-automation.co.uk, and discover how automated palletising can revolutionise your manufacturing process.
Find out more…
- Grantas Portable Cobot Palletising System: High-Performance Automation That Moves With You
- Manual vs. Automatic Palletising: A Comprehensive Comparison
- Manufacturing Efficiency: Why Every Second (and Every Pound) Counts
- The Hidden Costs of Downtime in Food & Beverage Production
- How Robotic Palletisers Deliver Fast ROI for Manufacturers